Unveiling the World of CNC Precision Lathe Parts Production
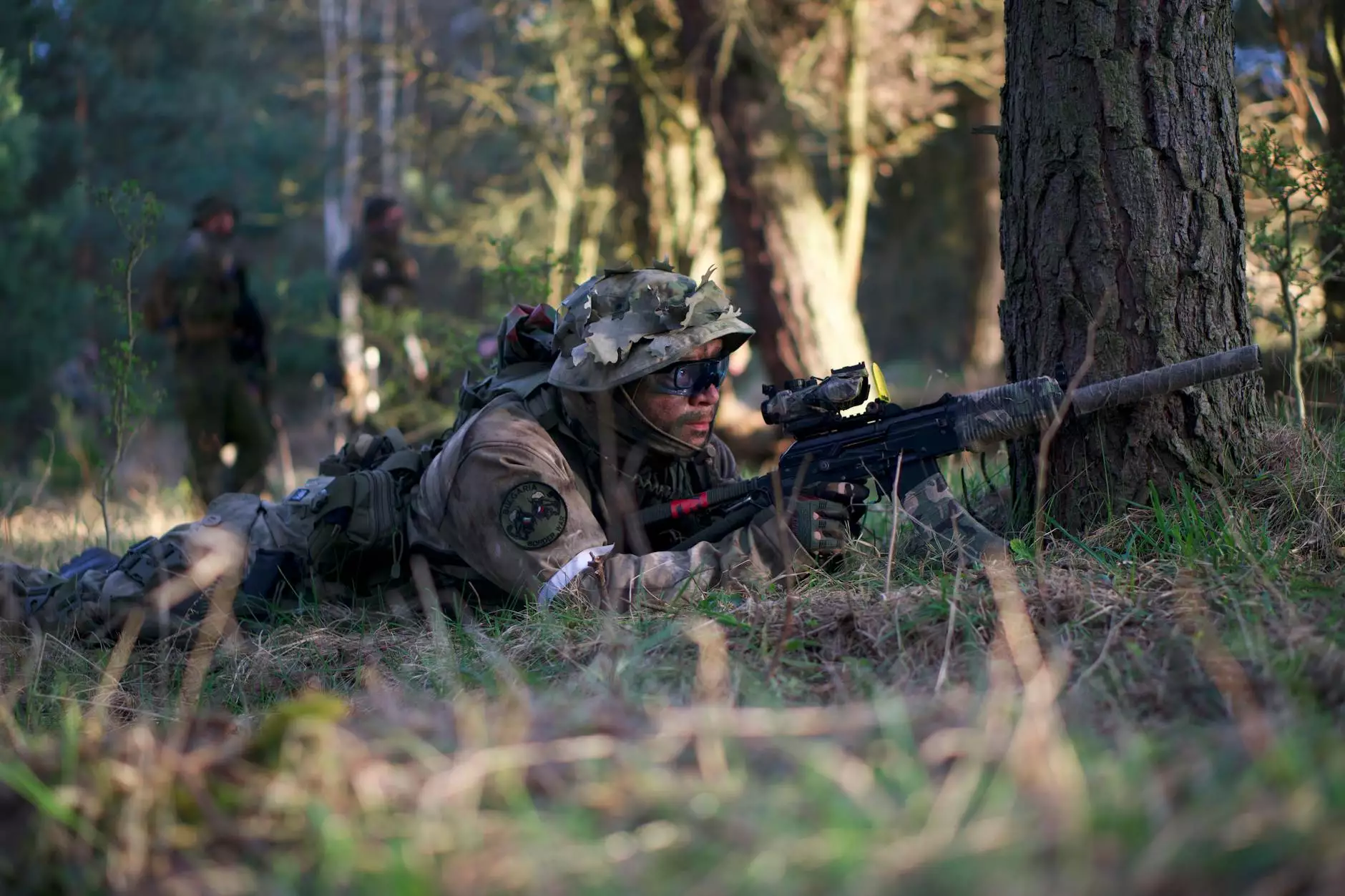
CNC (Computer Numerical Control) precision lathe parts play a pivotal role in various industries, including automotive, aerospace, and electronics. With the rise of advanced manufacturing technologies, China has emerged as a leader in the production of these intricate components. This article will explore the dynamics of a China CNC precision lathe parts factory, showcasing the innovations, processes, and benefits associated with these high-precision parts.
The Manufacturing Landscape in China
China is the global powerhouse in manufacturing, with a robust infrastructure and a rich pool of skilled labor. The CNC machining industry has seen significant advancements in technology and efficiency. Factories like DeepMould leverage cutting-edge systems and protocols that ensure precision and accuracy in every component produced.
Why Choose China for CNC Precision Lathe Parts?
Choosing a China CNC precision lathe parts factory like DeepMould comes with a plethora of advantages:
- Cost-Effectiveness: The lower labor costs in China reduce overall production expenses.
- Skilled Workforce: A vast number of skilled workers with technical expertise in CNC machining.
- High Production Capacity: Ability to handle large orders with quick turnaround times.
- Advanced Technology: Utilization of the latest machinery and software for superior quality control.
- Customization: Factories provide tailored solutions to meet specific client requirements.
Understanding CNC Lathe Parts
CNC lathe parts are integral components used in countless applications. What truly sets these parts apart is their design and manufacturing precision. By utilizing computer-generated commands, CNC lathes create parts that boast high tolerances and consistent quality.
Types of CNC Lathe Parts
Throughout the manufacturing process at a China CNC precision lathe parts factory, various types of CNC lathe parts are created, including:
- Shafts: Used as rotating components in machines.
- Bushings: Circular components that help reduce friction.
- Housings: Encasing parts that protect internal mechanisms.
- Adapters: Parts that connect different components seamlessly.
- Custom Parts: Tailored solutions for specialized machinery.
The CNC Machining Process
The process of manufacturing CNC precision lathe parts involves several stages, each critical to ensuring the end product meets the desired specifications. The steps typically include:
1. Design and Prototyping
The initial stage involves creating a detailed design of the part. Experienced engineers utilize CAD (Computer-Aided Design) software to create precise blueprints.
2. Material Selection
Choosing the right material is crucial. Factors such as durability, weight, and corrosion resistance come into play. Common materials include:
- Aluminum: Lightweight and corrosion-resistant.
- Steel: Offers high strength and durability.
- Brass: Known for its electrical conductivity and resistance to corrosion.
- Plastic: Used for lightweight applications.
3. Machining Operations
Using CNC machines, raw materials are meticulously shaped into parts. Different operations such as turning, milling, and drilling are executed to achieve the final dimensions.
4. Quality Control
Before parts are approved for sale, rigorous quality control tests are conducted. This ensures that each part meets the high standards expected by customers.
5. Finish and Delivery
After passing quality checks, parts are finished with the necessary treatments (such as anodizing or plating) and packaged for delivery.
Benefits of CNC Machining
Utilizing CNC precision lathe parts provides numerous advantages:
- Increased Efficiency: CNC machining significantly reduces production times.
- Enhanced Precision: CNC technologies ensure every part is produced with unparalleled accuracy.
- Flexibility: Quick adjustments can be made to accommodate changes in customer demands.
- Complex Geometries: CNC machining allows for intricate designs that would be difficult to achieve manually.
DeepMould’s Commitment to Excellence
As a leading China CNC precision lathe parts factory, DeepMould prides itself on quality, precision, and customer satisfaction. The factory has invested significantly in technology and personnel, ensuring that every aspect of the manufacturing process meets industry standards.
Technological Advancements at DeepMould
DeepMould employs state-of-the-art CNC machines that are updated regularly to incorporate industry innovations. This includes:
- High-speed Machining: Reduces production time while maintaining accuracy.
- Automatic Tool Change: Increases efficiency by minimizing downtime.
- Advanced CAD/CAM Software: Streamlines the design and manufacturing process.
Sustainability Practices
DeepMould is also committed to sustainable manufacturing practices. This includes:
- Waste Reduction: Minimizing scrap material through efficient machining techniques.
- Energy Efficiency: Utilizing machines that consume less power.
- Recyclable Materials: Sourcing materials that can be recycled post-production.
Client Testimonials
DeepMould has earned a solid reputation among clients across the globe. Here are some testimonials showcasing their positive experiences:
"The quality of the lathe parts we received from DeepMould exceeded our expectations. Their attention to detail truly sets them apart." - John D., Manufacturing Manager
"We rely on DeepMould for all our precision components. Their timely delivery and excellent communication make them an invaluable partner." - Sarah K., Product Developer
Conclusion
In conclusion, the potential offered by a China CNC precision lathe parts factory like DeepMould is immense. With advanced technology, skilled labor, and a commitment to quality, they provide industry-leading solutions for diverse manufacturing needs. As businesses continue to seek efficiency and precision, choosing DeepMould for CNC machining will undoubtedly position them for success in a competitive market.
For inquiries, you can visit DeepMould’s official website to learn more about their offerings and how they can assist in your next project.